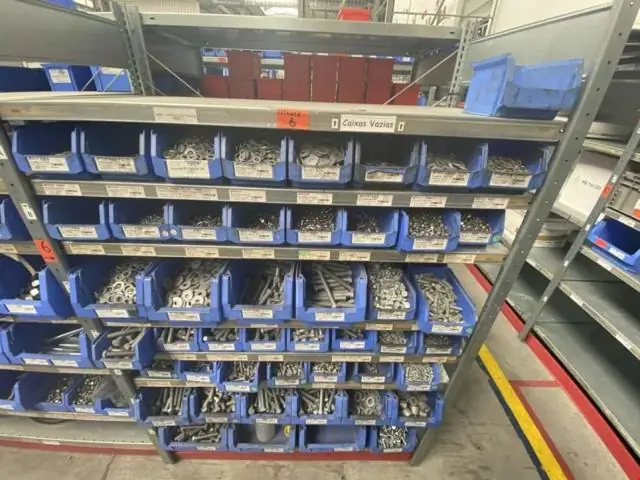
Table des matières:
2025 Auteur: Stanley Ellington | [email protected]. Dernière modifié: 2025-01-22 15:59
Kanban est une méthode visuelle pour contrôler production dans le cadre de Just in Time (JIT) et Lean Fabrication . Dans le cadre d'un tirage système il contrôle ce qui est produit, en quelle quantité et quand. Son but est de s'assurer que vous ne produisez que ce que le client demande et rien de plus.
Par conséquent, que signifie Kanban dans la fabrication ?
Kanban est un signal visuel utilisé pour déclencher une action. Le mot kanban est Le japonais et grossièrement traduit signifie « cartez-vous pouvez voir. Toyota a introduit et affiné l'utilisation de kanban dans un système de relais pour standardiser les flux de pièces dans leur juste-à-temps (JIT) production lignes dans les années 50.
De même, qu'est-ce que le système Kanban et comment fonctionne-t-il ? Kanban est un visuel système pour gérer travail au fur et à mesure qu'il avance dans un processus. Kanban est un concept lié à la production au plus juste et juste à temps (JIT), où il est utilisé comme un système qui vous dit quoi produire, quand le produire et combien produire.
Tout simplement, qu'est-ce que le système kanban de Toyota ?
?) (enseigne ou panneau d'affichage en japonais) est une planification système pour la production au plus juste et la fabrication juste à temps (JIT). Taiichi Ohno, ingénieur industriel à Toyota , développé kanban pour améliorer l'efficacité de fabrication. Kanban est une méthode pour atteindre JIT.
Comment le système Kanban est-il mis en œuvre dans la fabrication ?
Si vous souhaitez mettre en œuvre avec succès un système pull Kanban, votre équipe doit s'en tenir aux six pratiques fondamentales de la méthode:
- Visualisez le flux de travail.
- Éliminez les interruptions.
- Gérer le flux.
- Rendre les politiques de processus explicites.
- Maintenez des boucles de rétroaction ouvertes.
- Améliorez-vous en collaboration.
Conseillé:
Quels sont les sept déchets dans la fabrication?
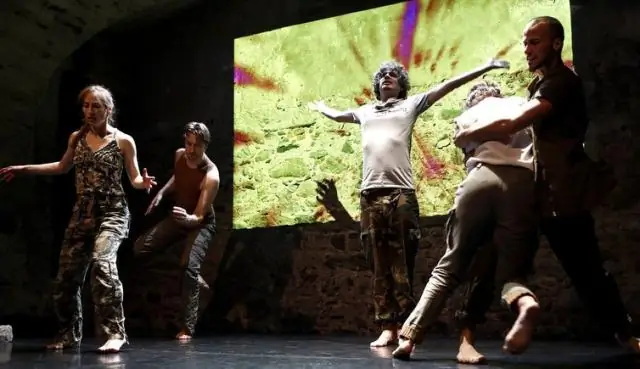
Dans le cadre du système de production au plus juste, sept déchets sont identifiés : surproduction, inventaire, mouvement, défauts, surtraitement, attente et transport
Quels sont les processus secondaires dans la fabrication?
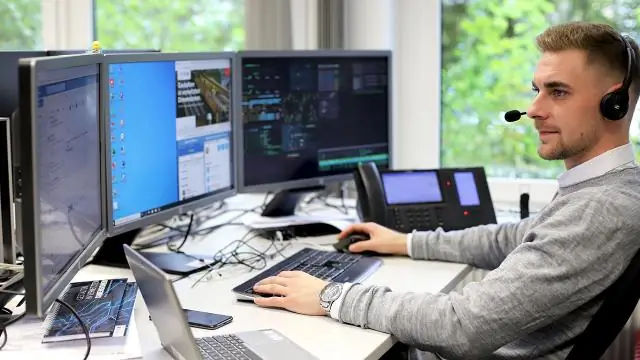
La dernière étape de la fabrication est appelée transformation secondaire. Il transforme les matériaux industriels en produits. Les processus sont effectués dans des usines qui emploient des personnes et des machines pour modifier la taille, la forme ou la finition des matériaux, des pièces et des assemblages
La publicité est-elle incluse dans les frais généraux de fabrication ?
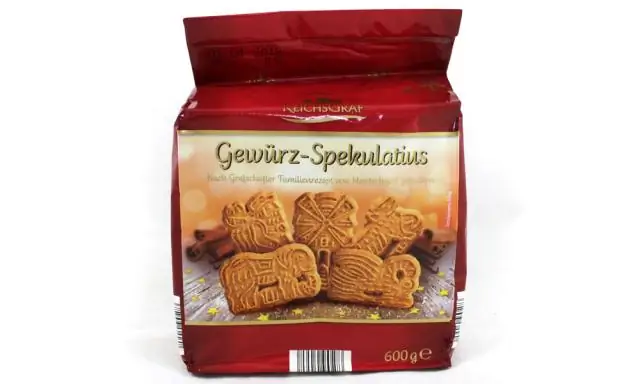
Ne fait pas partie des frais généraux de fabrication, n'est pas lié à la fabrication du produit. Exemples : tout ce qui se trouve au siège social de l'entreprise, tout ce qui concerne la vente du produit, les frais d'expédition, les salaires administratifs, les salaires des cadres, les dépenses de bureau administratif, les commissions de vente, la publicité, la recherche et le développement, etc
Est-ce que tous les détergents à lessive sont sans danger pour les systèmes septiques?
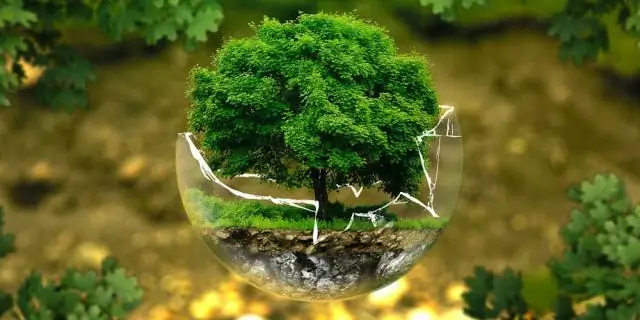
Pour un système conventionnel à gravité, utilisez une forme liquide de détergents à lessive. Cependant, pour une fosse septique aérée, vous pouvez utiliser soit un détergent à lessive liquide à haute efficacité (he) soit un détergent à lessive en poudre pour éviter une mousse excessive dans la chambre d'aération. Le détergent sans danger pour les fosses septiques doit avoir de faibles niveaux de tensioactifs
Quels sont les quatre attributs qui sont essentiels dans les systèmes d'entreprise aujourd'hui ?
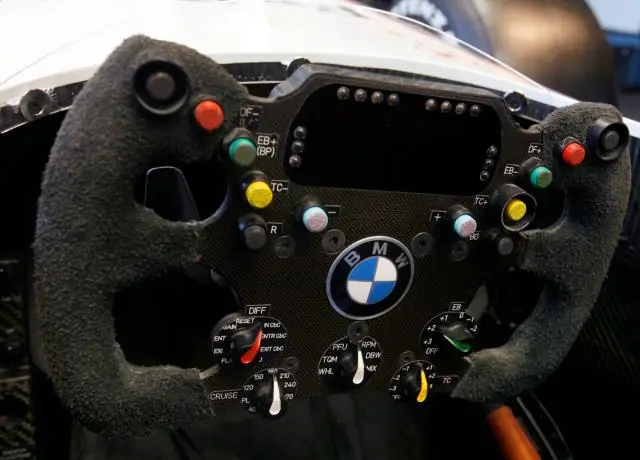
Nous sommes heureux que vous ayez posé la question : Ressources humaines. La gestion de vos employés est généralement la priorité numéro un. Gestion de la relation client. La gestion de vos clients et prospects est une autre facette importante de votre entreprise. L'intelligence d'entreprise. Gestion de la chaîne logistique. Système de gestion des stocks. Direction financière